前言
锂离子电池因其卓越的能量密度、功率输出和长寿命循环特性,在新能源动力系统和储能解决方案中扮演着核心角色。随着商业应用的不断进步,对锂离子电池的制造成本和性能要求也日益提高。电池的成本和性能在很大程度上受制于电极制造工艺的精细程度。因此,开发创新、可靠且成本效益高的电极制造技术对于推动锂电池的广泛应用至关重要。当前先进的商业锂电池主要采用制浆涂布的方式进行电极制造,这一过程涉及到将活性材料、导电剂、黏结剂及助剂均匀分散于溶剂中形成稳定悬浮液,随后在烘箱中干燥以蒸发溶剂。这一传统湿法电极工艺不仅能耗高,而且由于使用有机溶剂NMP,还需要部署昂贵且复杂的回收系统,进一步增加了制造成本。面对这些挑战,干法电极技术应运而生,以其无溶剂、制造成本低、电极机械强度高和对环境友好等优点,被认为是未来高性能储能器件开发中的关键技术。
1. 干法电极的提出
干法电极技术最早由美国公司Maxwell Technologies提出并发展。这项技术通过将活性材料粉末与导电剂混合后加入PTFE(聚四氟乙烯)粘接剂,然后施加高剪切力使PTFE原纤化后粘合电极膜粉末,最终通过挤压形成自支撑膜。Maxwell的干电极技术因其在成本、产品质量控制和性能表现上的优势而受到关注,特别是在提高电动汽车电池的行驶里程和降低成本方面具有显著潜力。特斯拉在2019年收购了Maxwell Technologies,从而获得了这项技术的专利和知识产权。
2. 干法电极制备流程
目前干法电极工艺主要有以下几种类型。
图1 几种干法电极工艺示意图及其特征
2.1 粉末压片法
粉末压片法如上图a所示,粉末压片法作为一种粉末成型方法,技术逐渐成熟并应用于储能领域,特别是全固态电池的电解质和电极。用于粉末压片的刚性模具和单向压制存在应力和密度分布不均匀的缺点、导致低密度及高孔隙率,也不适合规模化生产。
2.2 静电喷涂法
静电喷涂法如上图b所示,用高压气体预混活性物质、导电剂以及粘接剂颗粒,在静电喷枪的作用下使粉末带负电荷并喷至带有正电荷的金属箔集流体上,然后对载有粘接剂的集流体进行热压,粘接剂融化后会粘连其他粉末并被挤压成自支撑膜。静电喷涂法在干法电极工艺中是一种较为成熟的技术,适用于制备具有良好循环性能和稳定性的电极。
2.3 粉末喷涂法
粉末喷涂法如上图c所示,粉末喷涂法是一种成熟的技术,通过混合活性材料、导电剂和PVDF粘结剂,然后使用高压气体或静电喷涂将粉末沉积在集流体上。之后,在接近PVDF熔点的温度下进行热压,使粘结剂熔化并固定粉末。尽管这种方法适合roll-to-roll生产,但在大规模储能装置制造中的应用还不多见。
2.4 粘结剂纤维化法
粘结剂纤维化法如上图d所示,通过混合粉末、纤维化粘结剂、成型薄涂层和与集流体复合等步骤,形成具有纤维状结构的电极,以增强电池的机械和电化学性能,同时减少环境污染和制造成本。
干法电极工艺具有可扩展性,能够适应当前的锂离子电池化学体系以及先进的新型电池电极材料。大量商用负极材料(如硅基材料和钛酸锂(LTO))以及正极材料(如层状三元NMC、NCA、LFP、硫),证明了干电极工艺的稳定性和普适性。根据自支撑膜的成型方式,该工艺一般还可以分为:
粉末挤压成型:初步纤维化的混合粉末利用双螺旋杆挤出机进一步高速剪切使粘结剂纤维化并制备成自支撑膜,然后再和集流体复合。
粉末辊压成型:纤维化的混合粉末利用多级辊压机,差速辊压过程中的剪切力迫使粘结剂纤维化并制备成自支撑膜,然后再和集流体复合。
图2 粘结剂纤维化干法技术两种成膜方法
3. 干法电极优势
(1)干法电极不采用溶剂,无需涂覆后的烘箱和NMP回收装置。从而降低了总设备成本和运营费用。此外,干法电极工艺过程的产量更高,不仅降低成本和能源消耗也能带来更大的经济效益。
(2)电极中残留的溶剂还会与电解液发生副反应,使电极性能下降,如容量降低、产生气体和寿命缩短等,而干法电极无溶剂,可有效避免这类问题。
(3)湿法电极在溶剂蒸发过程中,粘合剂和导电剂会随着溶剂上浮偏聚在表面附近,而活性材料会沉淀,导致电极分层,这会损害电极中3D导电网络的构建,并降低活性材料和集流体之间的结合强度。而干法电极无溶剂,可以避免出现该问题。
(4)湿涂层通常溶剂蒸发过程中,电极容易出现裂纹,特别是厚电极,电极厚度会受到湿涂制造工艺的限制。干法电极工艺可以制备超厚电极。
(5)湿法电极工艺使用溶剂来溶解黏结剂,活性材料颗粒表面被黏结剂层包裹,会阻碍活性材料颗粒之间以及与导电剂颗粒的接触,导致电极导电性降低。干法电极在制作过程不使用溶剂,黏结剂以纤维状态存在,与活性材料颗粒表面仅为点接触,不影响活性材料颗粒间的内部接触,活性材料颗粒之间以及与导电剂颗粒的接触更紧密,电极的导电性好。而且Li+能够更好地在活性材料表面嵌脱,容量高,对高倍率放电有利。毛泽民等用四探针法测试了干法和湿法石墨负极极片的面电阻,结果显示: 干法极片面电阻为 4. 66 mΩ,较湿法工艺降低了 26%。
(6)与传统浆料涂层相比,干法电极涂层可以实现更高的结合强度。基于干法工艺的薄膜在保证结合强度的同时可以实现低粘合剂含量(<1wt%)。目前,先进的商业锂离子电池主要采用涂布工艺来制造电极,如图1所示的流程图详细描绘了这一过程。制浆步骤涉及将正极或负极活性材料、导电剂、粘合剂和辅助材料均匀分散在溶剂中,形成稳定的悬浮液。通常,去离子水用于正极材料的制浆,而有机溶剂N-甲基吡咯烷酮(NMP)则用于负极浆料的制备。涂布步骤则是将制备好的浆料通过涂布机均匀地涂覆在基底材料上,随后在长达数十米的烘箱中进行干燥。这一干燥过程在高温下进行,目的是迅速蒸发掉溶剂。干燥温度受到材料、溶剂(水或NMP)、涂布速度等多种因素的影响,通常超过100℃,导致显著的能量消耗。此外,在负极制造过程中,由于NMP可能对环境造成的危害,需要部署昂贵且复杂的回收系统,这进一步增加了生产成本。
4. 干法电极工艺的具体应用
4.1 固态电池中的应用
固态电池由于使用固体电解质,不再含有液体电解质,因此在生产工艺上有别于传统液态锂电池。干法电极工艺与固态电池的设计理念高度契合,能够在完全干燥的环境中进行生产,避免了溶剂残留的问题。例如,PTFE原纤维结构的粘结剂可以有效地增强电极的耐久性,防止活性物质颗粒的脱落。
4.2 4680大圆柱电池中的应用
特斯拉推出的4680大圆柱电池采用了干法电极技术,显示出显著的优势。干法工艺有助于降低电池成本,并提升电池的散热能力和充电效率。干法电极制备流程简化,生产速度快,能量密度高,特别适合这种大容量电池的制造需求。
5. 干法电极工艺的发展难点
(1)均匀度和一致性控制:干法电极成膜过程中,电极的均匀度和一致性控制是一个挑战,这涉及到工艺配比优化、混料工艺参数调整及工艺异常识别检测。
(2)工艺配比优化:在干法电极制造中,粘结剂含量的减少是一个技术难点,同时需要保证足够的膜片强度以适应高速连续制备。例如,清研纳科的目标是将负极粘结剂控制至0.7%,正极粘结剂含量低于1.5%,以实现更高效的低成本成膜性能。
(3)混料工艺参数调整:干法工艺的设计中,材料配方的调整能够优先保障成膜的均匀性和连续性,同时通过改性导电剂提高材料分散性。
(4)工艺异常识别检测:检测部分是挑战中的挑战,尤其是在干法电极成膜过程中均匀性的检测,这对于保证电池性能至关重要。
(5)设备与材料的协同创新:干法工艺的产业化不仅依赖于设备的技术突破,还需与材料研发形成协同创新。设备企业需要根据材料物化指标进行定制化优化,通过不断调整工艺参数实现最佳适配。
(6)规模化生产挑战:干法电极技术在大规模制造过程中存在挑战,包括小生产规模、特殊原材料处理要求以及与现有生产线的不兼容性。
*以上部分素材来源于网络,如有侵权,请联系删除
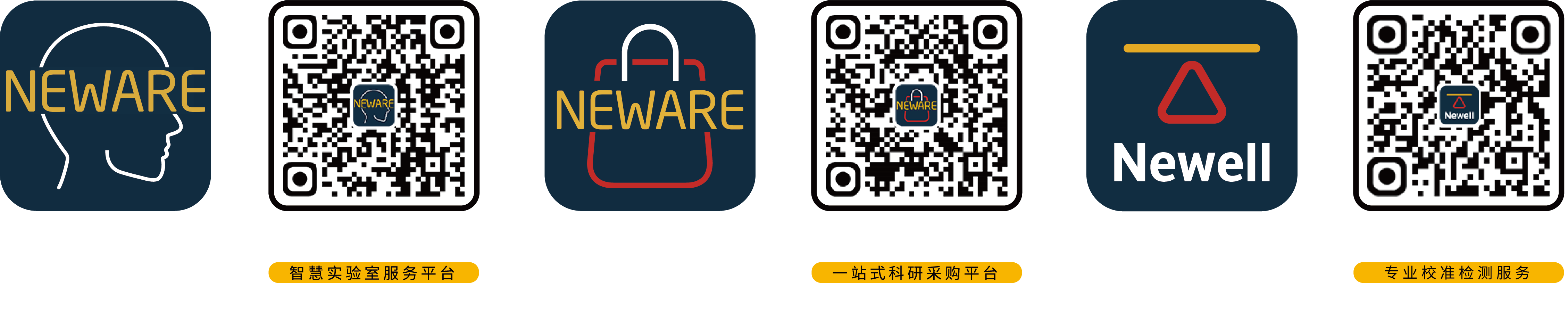