锂离子电池作为现代便携式电子设备、电动汽车和储能系统的核心组件,其性能直接影响这些设备的效率和寿命。压实密度是锂离子电池电芯设计中的一个关键参数,对电池的能量密度、功率性能和循环寿命具有重要影响。本文将详细探讨最佳压实密度对锂离子电池电芯设计的影响,并深入分析电芯的电化学和结构设计。本文旨在为电池设计工程师和研究人员提供全面的理论指导和实践参考,促进锂离子电池技术的发展。
1. 压实密度的基本概念
1.1 定义与重要性
压实密度指的是电极在一定压力下压实后的体积密度,通常以g/cm³为单位表示。压实密度的优化对锂离子电池性能至关重要。一般来说,在材料允许的压实范围内,高的压实密度可以增加单位体积内的活性物质含量,从而提高电池的能量密度。同时,合适的压实密度可以优化电极的孔隙结构,有助于减小电极材料在循环过程中的体积变化,提高离子和电子的传输效率,增强电池的循环倍率性能。
图1 电极辊压生产示意图
1.2 影响因素
影响压实密度的因素主要包括电极材料的性质、制备工艺和压实条件:
电极材料性质: 包括材料的粒径分布、形貌和比表面积等。
制备工艺: 包括浆料的混合、涂布和干燥工艺等。
压实条件: 包括压实压力、温度和时间等。
2. 压实密度对锂离子电池性能的影响
2.1 压实密度对电化学性能的影响
压实密度直接影响电极材料的孔隙结构和离子传输路径,从而影响电化学反应的动力学性能:
离子传输: 适中的压实密度可以提供良好的孔隙结构,确保电解液的充分浸润和离子的快速传输,优化电化学反应的动力学性能。
电子传输: 高压实密度可以提高电极的导电性,增强电子传输效率,有利于电化学反应的进行。
浓差极化: 适中的压实密度可以优化电极的孔隙结构,减少浓差极化现象,提升电池的电化学性能。
电阻极化: 高压实密度可以降低电极的内阻,减少电阻极化现象,增强电池的功率性能。
图2 常用材料真密度
2.2 极片过压对电池性能的影响
极片过压会造成电池容量降低,循环恶化,内阻增加等问题。极片过压会使球形三元材料大面积破碎,新产生的表面有很多脱离了二次球的一次小颗粒,它们要么因为没有接触到PVDF而从极片上掉落,要么因为没有接触到导电剂而使极片导电性能局部恶化。新表面的产生也使比表面增大,与电解液的接触面增大,副反应增加,从而造成电池性能降低,如电池气胀、循环衰减等。过压还会造成铝箔变形,极片脆片,容易折断,电池内阻增加。
极片孔隙率是指极片辊压后内部孔隙的体积占辊压后极片总体积的百分率。极片孔隙率过低会降低电解液量对极片浸润速率,影响电池性能发挥;过高会降低电池能量密度,浪费有效空间。孔隙率的测试可以采用压汞法、氮吸附、吸液法、估算法等,压汞法为常用方法。吸液法具体操作步骤如下:裁取适量极片,并计量所述极片的质量m;计量所述极片的体积V;将所述极片放置到容器中,所述容器内设置有电解液或其他溶剂(溶剂密度为ρ),将所述极片完全浸泡,并浸泡一定时间;取出所述极片,放置于滤纸上,吸拭至恒重,计量所述极片的质量m1;根据公式 ε=(m1–m)/ρV×100%,计算极片的孔隙率ε。估算法较为简单,根据材料的真密度与极片压实密度的差值可以估算极片的孔隙率。极片孔隙率计算方程式如下:
极片孔隙率(%) = (混合物真密度–极片压实密度) / 混合物真密度 × 100%
图3 常用材料压实密度与孔隙率
3. 压实密度优化方法
3.1 电极材料的优化
电极材料的性质对压实密度有重要影响。通过优化电极材料的性质,可以提高压实密度和电池性能:
粒径分布: 控制电极材料的粒径分布,可以提高材料的压实密度和导电性。采用纳米颗粒和微米颗粒的混合,可以优化材料的堆积密度和电化学性能。采用多级粒径分布,即在电极材料中混合不同粒径的颗粒,可以提高材料的填充密度。小颗粒可以填充大颗粒之间的空隙,提高整体的压实密度和导电性。
图4 不同粒度分布正极极片SEM图
形貌: 控制电极材料的形貌,可以提高材料的压实密度和电化学性能。球形颗粒具有较高的堆积密度,可以提高电极的压实密度。球形颗粒还可以减少电极在循环过程中的膨胀和收缩,提高电池的循环稳定性。片状颗粒具有较大的比表面积,有助于提高电极材料的活性和反应速率。通过优化片状颗粒的厚度和宽度,可以提高电极的压实密度和电化学性能。采用球形颗粒和片状颗粒的混合,可以优化材料的堆积密度和导电性。
比表面积: 控制电极材料的比表面积,可以提高材料的压实密度和电化学性能。高比表面积材料可以增加电极与电解液的接触面积,提高电池的功率性能。然而,高比表面积材料通常具有较低的压实密度,因此需要在比表面积和压实密度之间找到平衡点。
图5 不同形貌三元材料及其极片SEM图
3.2 制备工艺的优化
通过优化浆料制备、涂布工艺和干燥工艺,可以显著提高电极的压实密度:
浆料制备: 控制浆料的配方和混合工艺,可以提高电极的压实密度和电化学性能。浆料的配方对压实密度和电极性能有直接影响。合理选择和优化导电剂、粘结剂和溶剂的比例,可以提高浆料的均匀性和涂布质量。高效的混合工艺可以确保浆料的均匀性,减少气泡和颗粒的团聚现象。常用的混合设备包括行星搅拌机和高速剪切混合器等。优化导电剂和粘结剂的比例,可以提高浆料的均匀性和涂布质量。
涂布工艺: 控制涂布工艺的参数,可以提高电极的压实密度和电化学性能。控制涂布速度可以提高涂层的均匀性和质量。过快的涂布速度可能导致涂层不均匀,而过慢的涂布速度则会影响生产效率。涂布厚度对电极的压实密度和电化学性能有显著影响。优化涂层的厚度和均匀性,可以提高电极的电化学性能和机械强度。
干燥工艺: 控制干燥工艺的参数,可以提高电极的压实密度和电化学性能。优化干燥的温度和时间,可以提高涂层的机械强度和导电性。
3.3 压实工艺的优化
通过优化压实压力、压实温度和压实时间,可以提高电极的压实密度和电化学性能:
压实压力: 控制压实压力,可以提高电极的压实密度和电化学性能。适当增加压实压力,可以提高材料的堆积密度和导电性,但过高的压实压力可能导致材料的机械应力增大,增加材料的裂解和失效风险。而多级压实工艺可以逐步增加压力,减少材料的应力集中现象,提高电极的机械强度和稳定性。
压实温度: 控制压实温度,可以提高电极的压实密度和电化学性能。适当增加压实温度,可以提高材料的塑性和导电性,但过高的压实温度可能导致材料的热分解和性能下降。而采用热压实工艺可以在适当的温度和压力下,显著提高电极的压实密度和机械强度。
压实时间: 控制压实时间,可以提高电极的压实密度和电化学性能。适当延长压实时间,可以提高材料的堆积密度和导电性,但过长的压实时间可能导致材料的疲劳和性能下降。
4. 电芯电化学设计
4.1 电极材料选择
不同电极材料的物理化学特性不同,其适宜的压实密度也有所不同。正极材料如锂钴氧化物 (LiCoO₂)、镍钴锰氧化物 (NCM) 和磷酸铁锂 (LiFePO₄) 具有不同的密度和孔隙结构,对压实密度的要求也各不相同。负极材料如石墨和硅碳复合材料,其压实密度的优化也需要考虑材料的膨胀特性和循环稳定性。
图6 常用材料体系的压实设计范围
图7 石墨压实密度设计参考
4.2 电解液选择与电极压实密度的匹配
电解液的渗透性和离子电导率与电极的压实密度密切相关。高压实密度电极需要选择高渗透性的电解液,以确保电解液能够充分浸润电极材料,提高离子传输效率。用的溶剂包括碳酸乙烯酯 (EC)、碳酸二甲酯 (DMC) 和乙腈 (ACN)。锂盐的选择需要综合考虑其溶解性、导电性和热稳定性。常用的锂盐包括六氟磷酸锂 (LiPF₆)、四氟硼酸锂 (LiBF₄) 和双氟磺酰亚胺锂 (LiTFSI)。添加剂包括氟化锂 (LiF)、硫酰氟 (SO₂F₂) 和离子液体。
5. 电芯结构设计
5.1 电极设计
电极厚度:电极厚度与压实密度共同影响电池的能量密度和功率性能。优化电极厚度可以在保证高能量密度的同时,确保良好的离子传输和机械强度。
集流体设计:集流体的选择和设计对电极的导电性和机械强度有重要影响。铝箔和铜箔是常用的集流体材料,通过优化其厚度和表面处理,可以提高电极的导电性和粘附性。
5.2 隔膜设计
隔膜的孔径和厚度对电解液的浸润和离子传输有重要影响。通过优化隔膜的材料和结构,可以提高电池的安全性和循环寿命。隔膜材料的选择需要综合考虑其机械强度、热稳定性和离子导电性。常用的隔膜材料包括聚乙烯 (PE)、聚丙烯 (PP) 和复合隔膜 (PE/PP/PE)。隔膜的孔隙率直接影响电解液的浸润和离子传输性能。适中的孔隙率可以确保电解液的良好浸润和离子传输,优化电池的电化学性能。隔膜的厚度需要在确保机械强度的前提下,尽量减小,以减少电池的内阻,提高功率性能。通常,锂离子电池的隔膜厚度在20μm到30μm之间。
5.3 电芯组装工艺
电芯的组装工艺对压实密度和电池性能有重要影响。电芯结构优化包括极片的排布、极耳设计和壳体封装等方面。极片排布需要综合考虑电池的能量密度、功率性能和热管理等因素。常用的极片排布方式包括卷绕式和叠片式。极耳设计需要确保良好的电流传导和热管理性能。极耳的材料通常采用铜箔或铝箔,极耳的焊接质量直接影响电池的内阻和安全性。壳体封装需要综合考虑电池的机械强度、密封性和散热性能。常用的壳体材料包括铝合金和不锈钢,封装方式通常采用激光焊接或超声波焊接。电芯结构优化可以提高电芯的一致性和生产效率。
结论
最佳压实密度对锂离子电池电芯设计有着重要影响,直接决定了电池的能量密度、功率性能和循环寿命。通过系统了解压实密度的基本概念和影响因素,优化电极材料、制备工艺和压实工艺,可以显著提升电池的整体性能。希望本文能够为电池设计工程师和研究人员提供有价值的参考,推动锂离子电池技术的发展和应用。
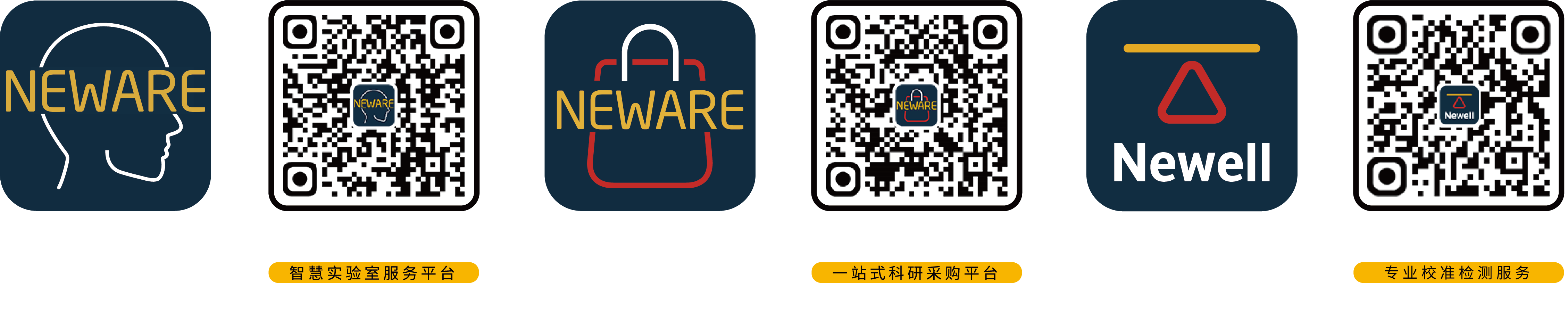